2PP technology enables freeform 3D microstructures
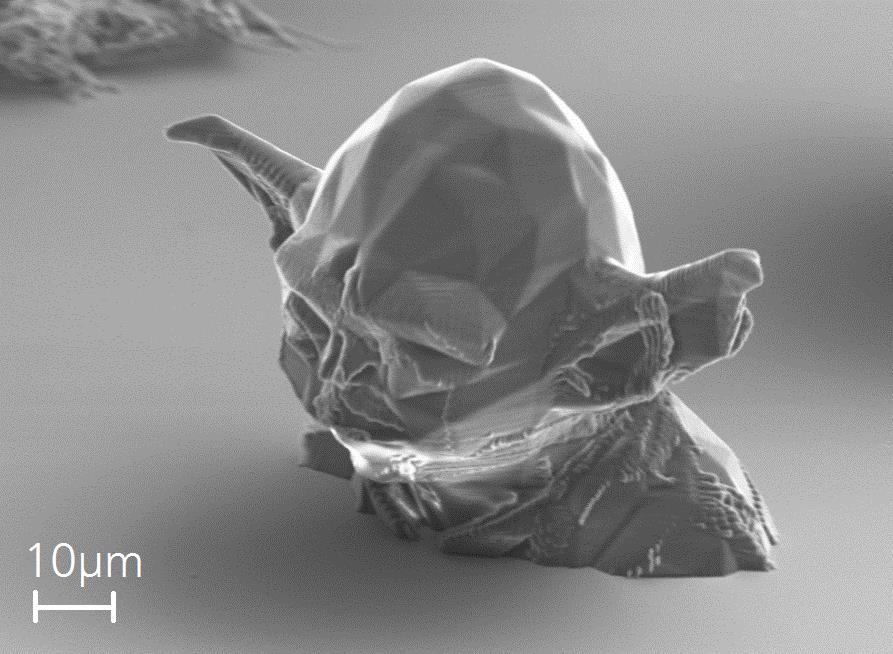
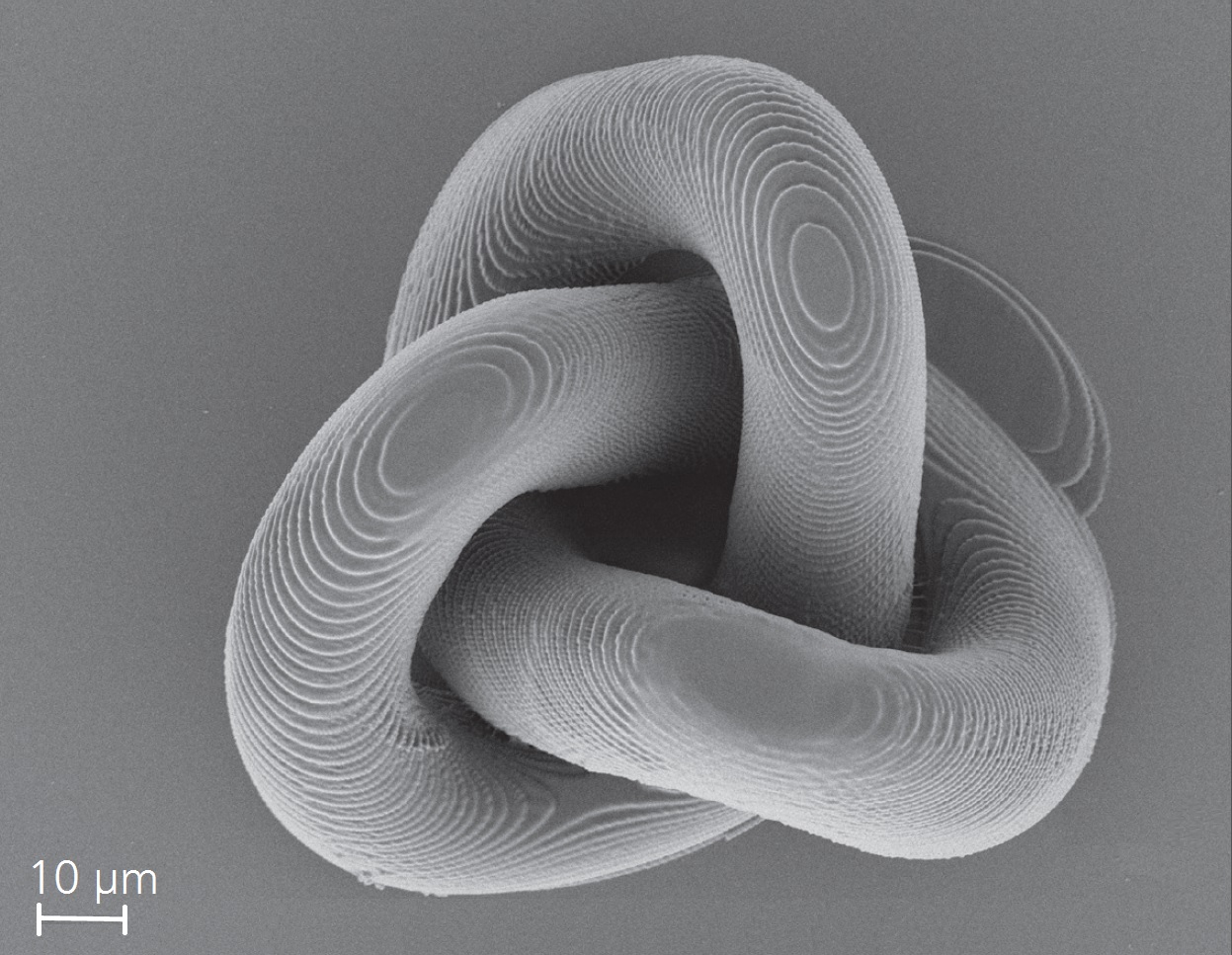
Arbitrary 3D microstructures
Two-Photon Polymerization (2PP) is suited for the fabrication of nearly any 3D micro- and macrostructures and structured surfaces. It uses tightly focused femtosecond laser pulses to confine the polymerization of a photopolymer to the focal volume. The underlying process – Two-Photon Absorption (TPA) – can only occur if the light intensity is sufficiently high so that the solidification of the material is located in the tiny focal volume. For 3D fabrication the focal volume is scanned in 3D space followed by a solvent wash to separate the remaining liquid photo-polymer from the solidified 3D structure. Thus 2PP offers a huge potential for innovative and very sophisticated microstructures and, compared to conventional methods, is an easy, fast, low cost and environmentally friendly procedure.
Customized fabrication with 2PP
With 2PP Fraunhofer ISC fabricates customized micro- and macrostructures for various optical applications. This includes new designs for metamaterials and photonic crystals, optical waveguide structures for interconnects or diffractive multi-level and continuous-level optical elements. The precision of the generated 3D structures is extremely high (< 1 µm) and the feature size can be as low as 100 nm. Using special illumination strategies the high accuracy can also be reached for macrostructures with heights up to 2 cm.
In the project FOWINA Fraunhofer ISC and Fraunhofer IIS currently develop complex angular filter structures to realize color sensors directly on chip level. The sensors measure optical spectra independently of the incidence of the light and can be employed in smartphones or LED lighting in cars.
In a second project – µFLO – Fraunhofer ISC and Fraunhofer ILT are working on freeform 3D microlenses and microfluidic components for optical or medical devices. To get aspheric or entirely freeform surfaces with superior precision and higher optical quality compared to other methods, they combine 2PP, selective laser etching (SLE), and laser polishing (LP).
Adjustable properties with ORMOCER®s
For both projects FOWINA and µFLO the Fraunhofer institutes use inorganic-organic hybrid polymers (ORMOCER®s) developed by Fraunhofer ISC. ORMOCER®s excel with their outstanding optical properties. These stem from the underlying inorganic (glass-like) molecular structure which is also responsible for very high chemical, thermal and mechanical stability. ORMOCER®s maintain their key properties (refractive index, low, absorption) even under harsh conditions and show no yellowing. Additionally, their properties can be tailored to application-specific needs by adaptation of the molecular structure during the synthesis. Apart from Two-Photon Polymerization, ORMOCER®s can be processed with conventional UV lithography, Nanoimprint Lithography (NIL) and other printing and replication techniques.
At the German Pavilion, Photonics West 2016 (Booth# 4629-25), Fraunhofer ISC provides information about materials development and characterization, process techniques and their optimization, aging studies, and strategies for improved fabrication.
More Information: Optical materials and components, Fraunhofer ISC
Letzte Änderung: